En marche vers l’avenir : comment Kamik est devenu vert
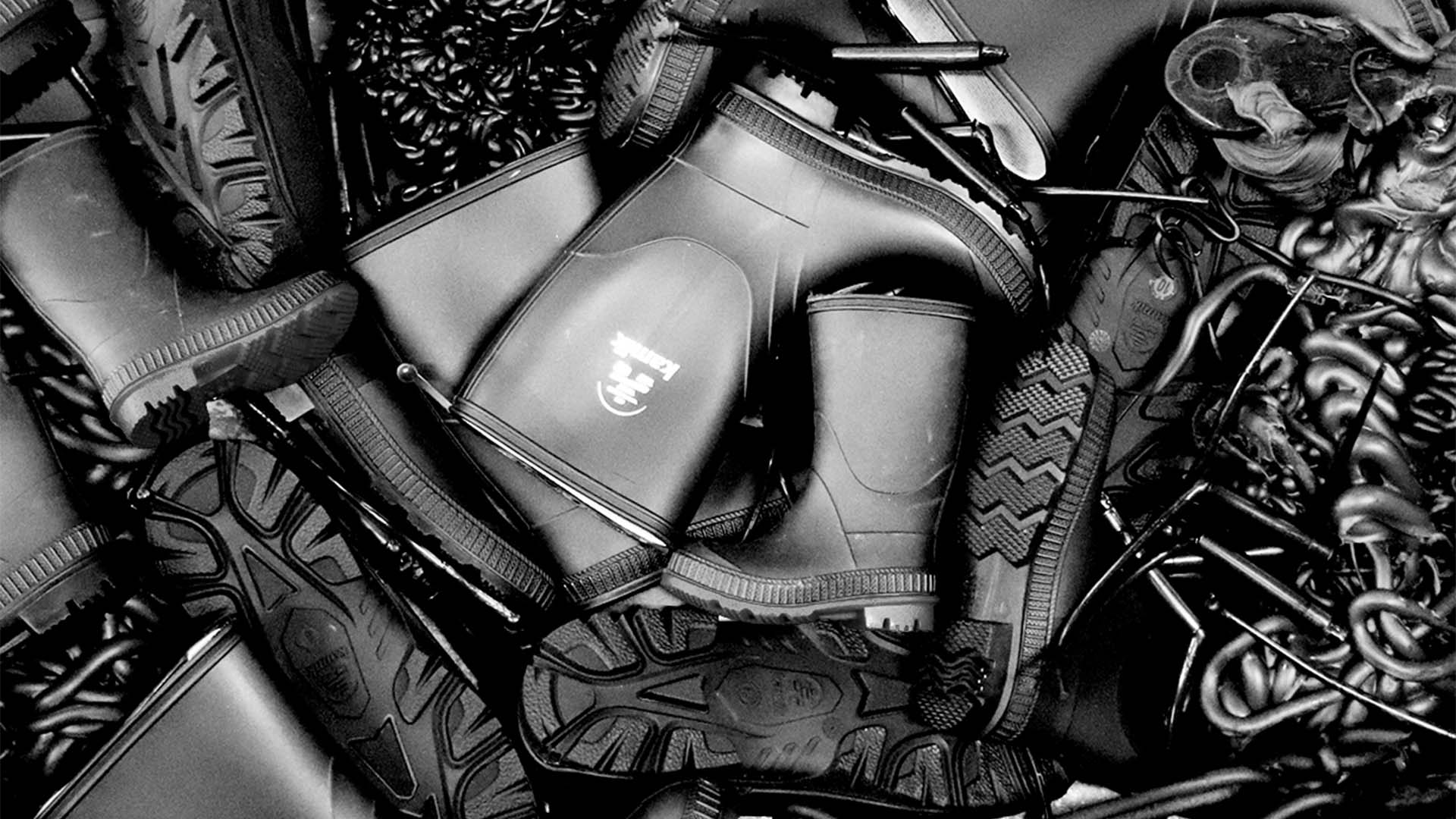
Cet article s’inscrit dans la collection « VOIR GRAND ».
Par Gabrielle Anctil, journaliste
Steeve Côté, ing., chef de l’exploitation chez Kamik, revient tout juste d’un voyage en Asie, où il a pu découvrir de nouveaux textiles et matériaux, dont une grande partie sont faits de matières recyclées. Son but : dénicher un produit aussi performant qu’une matière neuve, à prix compétitif.
Kamik utilise des produits recyclés depuis fort longtemps, notamment pour produire les feutres de ses bottes d’hiver. Le recyclage et la réutilisation des matériaux sont au cœur des activités de l’entreprise — au point où l’usine de la compagnie à Lachine ne génère que deux bacs de recyclage par semaine, qui contiennent « surtout les déchets des lunchs des employés », souligne Philippe Bichai, ing., directeur du bureau de gestion de projet et de l’environnement et conformité chez Kamik.
Steeve Côté explique la motivation qui a mené l’entreprise à faire un virage vert. Plutôt que de se lancer dans un baratin à saveur d’éco- blanchiment, il dit en toute franchise : « C’est là que le marché nous amène. En Europe, surtout en Allemagne, les clients nous poussent vers cette réalité. » Car, bien que l’environnement soit une préoccupation pour Kamik depuis fort long- temps, l’ingénieur demeure réaliste : le prix des matières premières joue un rôle lorsqu’on conçoit un produit. « Le client veut des produits bons pour l’environnement, mais il n’est pas toujours prêt à payer le prix », constate-t-il.
Malgré ce discours sans prétention, force est de constater que Kamik travaille d’arrache-pied à verdir ses opérations.
« C’est là que le marché nous amène. En Europe, surtout en Allemagne, les clients nous poussent vers cette réalité. »
Steeve Côté, ing. – Chef de l’exploitation chez Kamik
Un petit pas pour Kamik
Le processus de fabrication des feutres de bottes est peut-être le meilleur symbole de l’attachement de Kamik pour les réductions de coût à l’empreinte verte. « Au début, on utilisait de la fibre vierge, raconte le chef de l’exploitation. Les fournisseurs ont tenté de trouver des matières qui permettraient de réduire les coûts. C’est comme ça qu’on a fait la transition vers les matières recyclées. » Depuis, les doublures de bottes sont faites à partir de plastique réutilisé — initialement issu de bouteilles de plastique, maintenant de rejets de moulage de l’industrie automobile.
La fabrication de ce tissu est somme toute assez simple. Dans une vidéo produite pour la série de télé canadienne How It’s Made, on peut voir les feutres s’étoffer : des ballots informes sont distribués dans une machine qui les sépare en longues bandes de tissu. Le tout est empilé en plusieurs couches, puis percé par des aiguilles à la tête crochetée. « C’est toujours comme ça que le feutre est fabriqué », résume Steeve Côté, qui signale que ce processus ne nécessite aucun additif.
L’exemple des feutres illustre bien l’effort d’innovation tranquille de l’entreprise. Grâce à ce choix de matériau, toutes les retailles peuvent être réutilisées simplement en les remettant dans la machine. Résultat : un pro- cédé zéro déchet, sans trop d’embûches.
Récemment, une réorganisation de la chaîne de production — encore une fois pour réduire les coûts — a aussi permis de diminuer les émissions de GES liées à la production des feutres. « Avant, une partie de la couture se faisait à Mississauga et une autre à New Hamburg, en Ontario, précise Philippe Bichai. On a tout rapatrié à Montréal, ce qui diminue l’impact des déplacements. »
« La mentalité ici est qu’on ne jette jamais rien. On peut tout réutiliser. »
Philippe Bichai, ing. – directeur du bureau de gestion de projet et de l’environnement et conformité chez Kamik
Un pas de géant pour la planète
Chaque année, 360 000 bottes de pluie noires sortent de l’usine canadienne de la compagnie, sans compter les semelles de même cou- leur fixées sur des produits variés. Possédez- vous des bottes Kamik ? Si oui, observez bien la semelle : est-elle noire ? « Quand c’est du caoutchouc, si c’est noir, c’est que la matière a été recyclée », indique Steeve Côté. « Le caoutchouc naturel n’est pas recyclable, alors que son pendant synthétique l’est à 100 %, », rapporte Philippe Bichai. Il nuance cependant : « Ça ne veut pas dire qu’on peut mettre nos bottes au recyclage ! Mais nous offrons un programme qui permet aux consommateurs de nous envoyer leurs bottes usées. On les déchiquette et on les remoule. »
La compagnie a entamé la transition vers le caoutchouc synthétique il y a une quinzaine d’années, mentionne l’ingénieur. Résultat : maintenant, en plus d’offrir un produit pouvant être remoulé presque à l’infini, personne à l’usine ne porte de masque, l’odeur de ce matériau étant bien plus agréable que celle du caoutchouc naturel.
Quoi d’autre ? « On a implanté un système à boucle fermée pour l’eau, dit Philippe Bichai.
Aujourd’hui, on recycle 90 % de l’eau de l’usine. On utilise aussi l’air de l’extérieur pour refroidir l’eau. Ça permet de sauver l’équivalent du contenu de 15 ou 16 piscines olympiques par an. » À cela s’ajoute un emballage recyclable certifié FSC, l’utilisation d’un additif à base d’algue produit par la compagnie Bloom et un projet, en collaboration avec Canadian Tire, de bottes fabriquées avec des pneus recyclés. « C’est un peu plus compliqué parce que leur résistance à la flexion n’est pas excellente, précise Philippe Bichai. On se demande s’il ne serait pas mieux d’incorporer le matériau dans la semelle. »
« La mentalité ici est qu’on ne jette jamais rien, résume Philippe Bichai. On peut tout réutiliser. » En quête de réduction de coût et animé d’un désir profond de jouer un rôle positif pour la planète, Kamik, qui a célébré en 2023 son 125e anniversaire, continue à faire son petit bout de chemin.
___________________________________
Certifier pour mieux verdir
Impossible pour Philippe Bichai de dresser la liste de toutes les certifications obtenues par Kamik : il y en a trop. En plus de celles qui sont reconnues à l’international, comme la Clean Recycling Initiative ou le Higg Index, « de plus en plus de gros clients demandent de visiter nos usines pour nous attribuer leur propre certification », un processus plutôt coûteux, selon le directeur du bureau de gestion de projet et de l’environnement et conformité chez Kamik.
De fait, les exigences liées à l’obtention d’un sceau vert entrent parfois en contradiction avec les objectifs de l’entreprise. « On veut doubler de taille d’ici cinq ans, indique Philippe Bichai. Mais pour obtenir la certification Carbon Neutrality, on doit encore diminuer nos émissions de GES, qui sont déjà très faibles. »
À cette liste s’ajoutera peut-être prochainement une analyse de cycle de vie. « Pour le moment, c’est plus technique que ce dont on a besoin. Mais on sait que si une personne porte nos bottes pendant 10 ans et qu’elle prend la peine de nous les envoyer ensuite pour être recyclées, il n’y aura pas tellement d’impact environnemental à long terme. »